Anodes
Protection
Low Profile
Anodes
Fitting or replacing your anodes consistently will give your hull the best chance of a healthy long life, which benefits both you, your boat and your pocket in the long run.
Anodes on both the sides and the base-plate will enable a maximum 4 to 5ft radius of protection to be achieved by each anode, prolonging the health of your hull.
The repurposing of anodes which are not down to a 30% level is a good idea and we will only charge for rewelding them to your hull if we need to remove. Supply your own anodes and we will fit.
- Low profile 2.7kg for sides and base
- All anodes are welded
- Bring your own we will fit for you
- Repurposing anodes means only re-welding is required
Your boats anodes are assessed out of water and it is totally up to you what you do from that point.
Each anode should be replaced by the time it reaches 30% of it’s original size at the very latest.
Pricing
- £ 95.00 Low Profile (fitted)
- £ 35.00 Cust supply (welding only)
- Removal of tags FOC


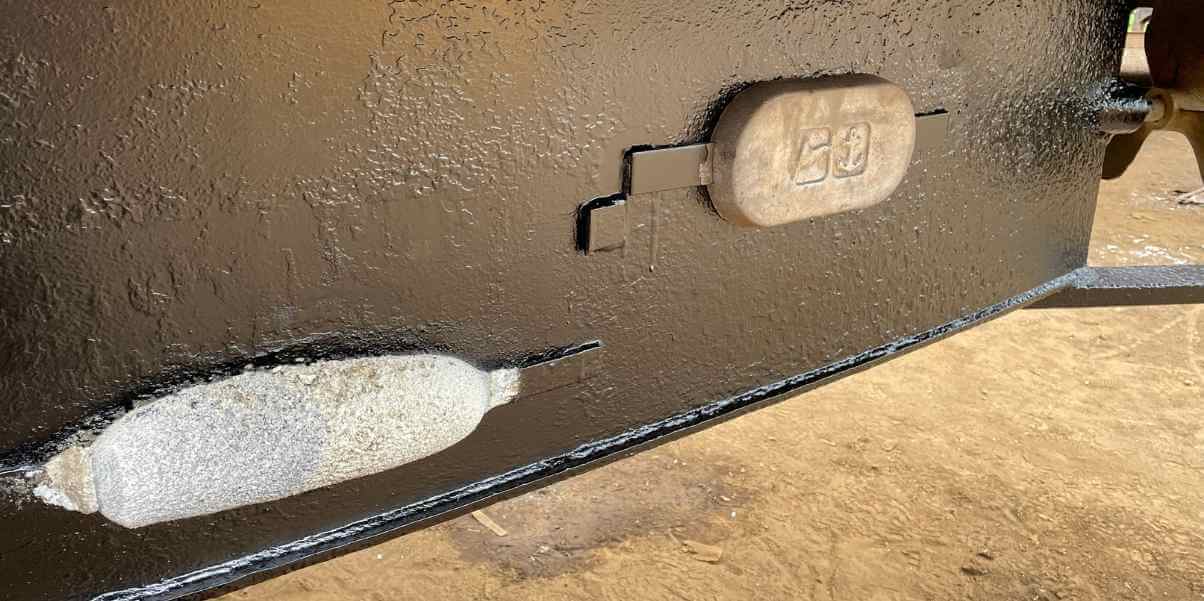
Emma N
Why Anodes
Over the 20 years P&S Marine has been in business, the difference in the condition of hulls with anodes regularly fitted and those without, is enormously telling.
A typical canal boat will be made up of a number of different metals that need protecting. For example, mild steel, stainless steel, bronze and brass. By introducing a less noble metal to the hull to act as a sacrificial material, it ensures that the important metals are not affected by electrolysis which is caused by the movement of water against them.
It is a myth that you do not need to protect the baseplate!! It is just as important as the sides and we recommend anodes are fitted every 8 to 10ft with 2 at the bow and stern.
Anodes are fitted or replaced after hull blacking.
Just remember the anode is a small sacrifice compared to your hull!
Call to Book:
0800 170 7276
Email To Book:
hello@pandsmarine.co.uk
Other Services
Cranage
Hardstanding
Engine Servicing
Hull Blacking
Two coats of SML bitumen for the
hull of your vessel
Steelwork
Grit Blasting
FAQ
GLORIA: DO NOT USE THE TOP QUESTION - IT IS INVISIBLE
Do I really need anodes?
Yes. Of course, it’s totally up to you but we highly recommend anodes for protecting the whole hull.
I've been told anodes are not needed on the baseplate. Is this true?
No. The baseplate is just as susceptible if not more to corrosion as the sides. Steelwork is much more expensive than anodes.
Why do you use magnesium anodes?
What if I sail in brackish water?
Your magnesium anodes will corrode much quicker if you are constantly in brackish or sea water due to the salt content. Brackish water is found in estuaries where the rivers meet the sea. It is unlikely that the majority of canal boats will spend a lot, if any time in these areas. If you know that this is not the case, please speak to us directly and we will see how we can help. Of course you can always source your own anodes and we can weld them for you.
How many will I need?
We always assess your need for anodes once you are out of the water. We need to see which are corroded beyond further use and which can be repurposed. We recommend an anode every 8 to 10ft along the baseplate and every 5 to 6ft along the sides.