Grit Blasting
Iron Silicate
High Pressure Compressed Air
For optimal surface roughness and removal of contaminates
Grit Blasting
Grit blasting, sand blasting or abrasive blasting are all terms used to describe the operation of forcibly propelling a stream of abrasive material against a surface under high pressure to smooth a rough surface, roughen a smooth surface, shape a surface or remove surface contaminants.
We use iron silicate to roughen, which is actually better for the environment than quarrying natural rocks. It’s purposely produced during the refining and recycling processes of copper.
Grit blasting slots are limited due to the impact on the surroundings in the yard, the team and other clients. We do NOT grit blast cabins.
We only take bookings between April and October due to cold weather conditions affecting the process.
- High pressure surface preparation
- You need a primer before blacking
- It’s noisy and messy
- Limited slots available. Slots are generally 2 – 3 weeks long
Remember grit blasting can reveal pits and other damage to the hull, which will then need to be addressed before painting. We do offer steelwork and welding services, but this is discussed and quoted on a one to one basis.
Although we do not offer Epoxy you may wish to still grit blast prior to hullblacking using SML bitumen.
Pricing
Grit Blasting per foot (inc. VAT) does not include cranage
- £ 70.00 p/f Narrow beam Band 1 | Whole hull
- £ 80.00 p/f Wide beam Band 2 | Whole hull
- £ 90.00 p/f Wide beam Band 3 | Whole hull
- £ 100.00 p/f Wide beam Bands 4 | Whole hull
- Part hull blasting also available
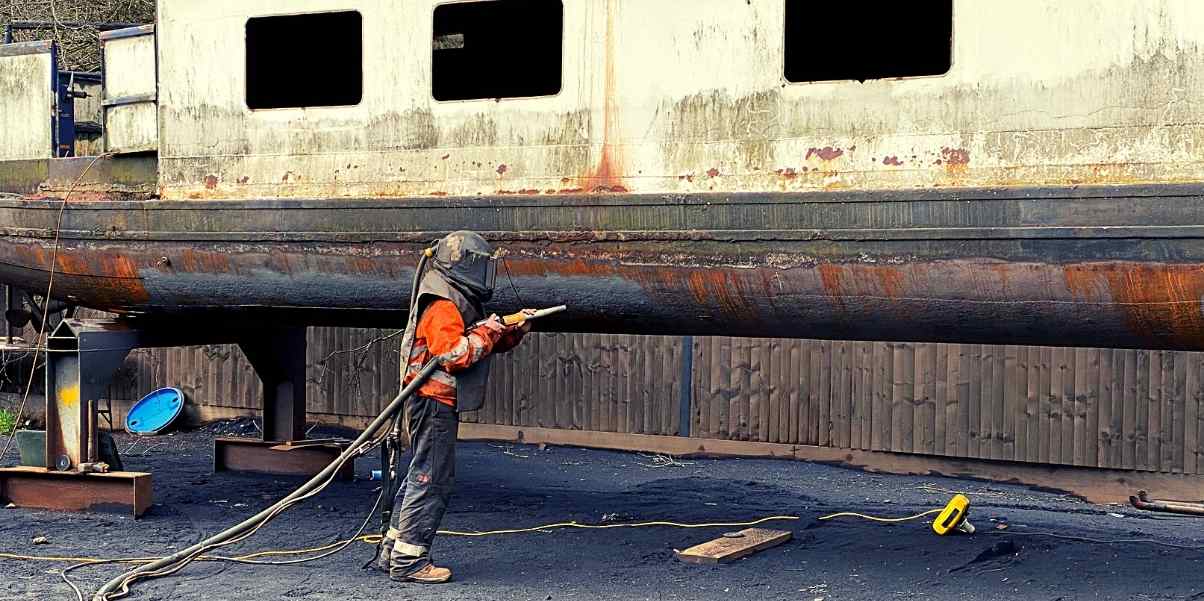

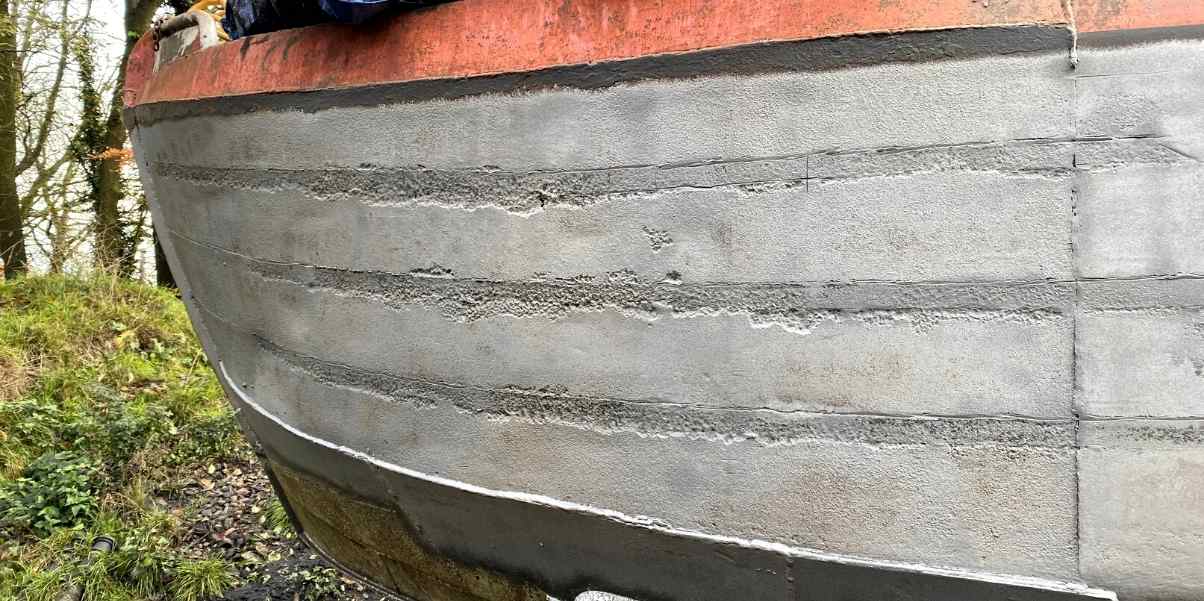

“Just left having had loads of brilliant work done. All really helpful, knowledgeable and easy to work with. Had grit blasting, pad welding, 3 coats of epoxy (DIY), other fixes around the boat including the sceptic tank removed, woodworking, chemical fixes and other welding jobs. Learned a lot from everyone as well. Had a great time (4 weeks) in the yard and would definitely recommend. As solo woman on a boat this is really refreshing. (Sept 2023)”
Hannah Calascione
Call to Book:
0800 170 7276
Email To Book:
hello@pandsmarine.co.uk
Other Services
Cranage
Hardstanding
Engine Servicing
Anodes
Steelwork
Hull Blacking
hull of your vessel
FAQ
GLORIA: DO NOT USE THE TOP QUESTION - IT IS INVISIBLE
Do I need to grit blast?
How long will it take to grit blast?
Is it something I can do myself?
What if I want to apply Epoxy after grit blasting?
What are the Bands?
Band 1 – Narrow boat up to 7ft
Band 2 – 4 Wide beam 7ft 1in to 14ft
Prices start at a minimum 40ft in length